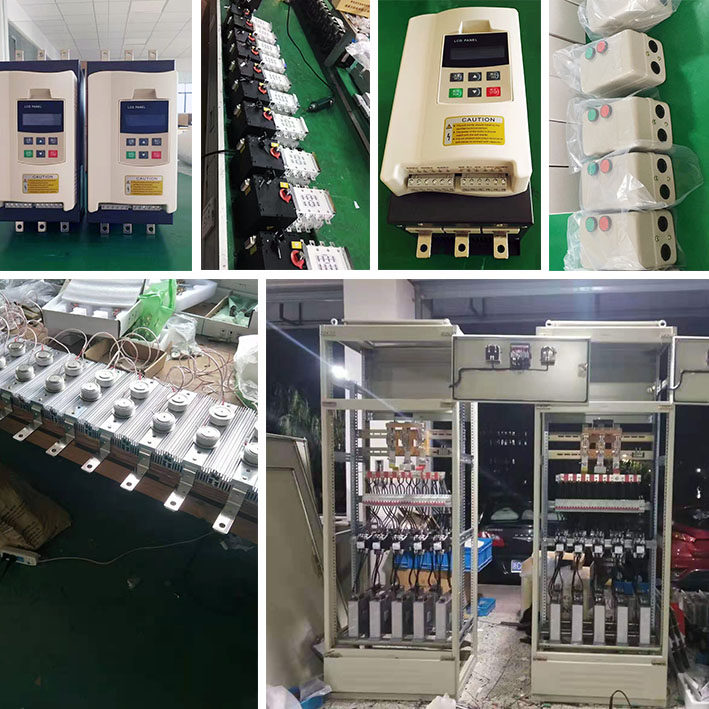
2025欢迎访问##海南MT-DB140S67-U单相电压表价格
湖南盈能电力科技有限公司,专业仪器仪表及自动化控制设备等。电力电子元器件、高低压电器、电力金具、电线电缆技术研发;防雷装置检测;仪器仪表,研发;消防设备及器材、通讯终端设备;通用仪器仪表、电力电子元器件、高低压电器、电力金具、建筑材料、水暖器材、压力管道及配件、工业自动化设备销;自营和各类商品及技术的进出口。
的产品、的服务、的信誉,承蒙广大客户多年来对我公司的关注、支持和参与,才铸就了湖南盈能电力科技有限公司在电力、石油、化工、铁道、冶金、公用事业等诸多领域取得的辉煌业绩,希望在今后一如既往地得到贵单位的鼎力支持,共同创更加辉煌的明天!
再来说说汽车充电系统的工作过程。当我们打点火关,蓄电池向汽车各用电设备供电,电控系统自检,为发动机启动好准备;同时蓄电池也会向发电机转子励磁电流,为发电机发电好准备;当我们把点火关拧到启动档时,起动机接通,蓄电池给起动机启动电流,带动发动机转动,并使发动机点火启动。当发动机正常工作后,发电机也随发动机高速运转,定子绕组切割转子绕组的磁力线,产生三相交流电流,经过硅整流后变成直流电向外输出,给汽车的用电设备使用,多余的电能用来给蓄电池充电。
印刷电路板(PCB)是集成各种电子元器件的信息载体,在电子领域中有着广泛的应用,其质量直接影响到产品的性能。在PCB过程中,PCB上的元器件普遍采用表面贴片技术。随着电子科技技术的发展和电子业的发展,电子产品趋于更轻、更小、更薄化。PCB板作为现代电子设备的重要组成部分,由于贴片元器件体积小,密度大,这就要求PCB板的集成度进一步提高。为了保证电子产品的性能,PCB板缺陷检测技术已经成为电子行业中非常关键的技术。
如电子设备不满足噪声限制规则,则产品就不能出和使用。由于上述种种原因,在电源设备中必须要设计使用满足要求的电网噪声滤波器。EMI噪声和滤波器的类型在电源设备输入引线上存在二种EMI噪声:共模噪声和差模噪声,如所示。把在交流输入引线与地之间存在的EMI噪声叫作其共模噪声,它可看作为在交流输入线上传输的电位相等、相位相同的干扰信号,即的电压V1和V2。而把交流输入引线之间存在的EMI噪声叫作差模噪声,它可看作为在交流输入线传输的相位差180°的干扰信号,即中的电压V3。
在该电源接入电网后,会对电网内其他的用电设备产生影响,导致电网内直流电源的输出纹波较高,无法正常测试。即使移除地线的连接,将交直流源各自分至很远的位置,并通过不同的空接入后,干扰依旧存在。某品牌电源对电网内直流源输出干扰波形而在相同的测试环境使用APM全天科技可编程交流电源后,直流源输出纯净稳定,无任何影响。APM全天科技可编程交流电源通过严苛的EMC测试等级,符合欧盟电磁兼容指 lassA以及FCCCFR47第15部分的要求。
电源模块以高集成度、高可靠性、简化设计等多重优势,受到许多工程师的青睐。但即便使用相同的电源模块,不同的用法也会导致系统的可靠性大相径庭。使用不当,非但不能发挥模块的优势,还可能降低系统可靠性。相信各位电路设计者在阅读DC-DC隔离电源模块的数据手册时,时间关注的往往是首页的电源参数,如功率、输入电压、输出电压、效率、工作温度、耐压等级等……但其实在实际应用中,数据手册中的“电路设计与应用”一节内容同样重要,它为用户在实际外围电路设计过程中了宝贵的参考电路经验。
电动汽车放电对电力系统的影响研究发现,EV入网比建设调峰电厂或机组更加经济,目前也有相关文献研究V2G技术的可行性与潜在效益。车网互联的概念将带来新的补偿理念,如果采取正确合理的调度和引导,用电动汽车吸纳过剩的可再生能源、平抑波动,有助于实现供需平衡,同时可以扩大电力市场、降低峰谷差、为电力系统备用。但是考虑电价因素的电动汽车有序充电和与可再生协调互补、或者参与调频、作为旋转备用等方面的综合调度策略并没有成熟的研究,有待进一步的探索和发展。
按此计算,两机器人 多的测量点数为:(13-2)/2.5=88个点。测量点的选择、模拟与确认整个焊装生产线共有四个关键的总成状态:侧围总成、发动机舱总成、地板总成及车身总成。我们只采用了一套在线检测系统,即白车身的在线检测系统,测量的点数越多,在线监控的视野也就越广阔。在计算机之前,以固定式三坐标测量点为基础,并根据测量点的重要性,经过计算机三维模拟及现场调试,共确定了77个测量点。检测的实现及可实现的功能检测过程如所示,白车身在滑撬上运动到检测工作站停下并,线控制器给检测站控制器发“到位”信号站控制器给机器人发“车型”及“启动”信号机器人接到信号后始工作,机器人在每个测量点向测量控制器发“测量请求”和“测点ID”信号,等待测量控制器发回的“测量完成信号”测量系统接到信号后始测量并记录数据,然后传递到测量分析软件进行,测量结束后向机器人发“测量完成”信号机器人收到“测量完成信号”后始向下一测量点运动,至此完成全部待测点的测量。